The estimated revenue loss due to equipment downtime can vary widely depending on the industry, the equipment’s size and complexity, and the downtime’s duration. In the manufacturing industry alone, unplanned downtime costs companies as much as $260,000 an hour, according to a study conducted by analyst firm Aberdeen Research1.
Equipment downtime can be avoided by implementing preventive maintenance measures, which can help identify potential problems before they become more severe and lead to equipment failure.
What is preventive maintenance?
Preventive maintenance (PM) is designed to prevent equipment failure before it occurs, rather than waiting for equipment to fail and then repairing it. The goal of preventive maintenance is to identify potential issues with equipment and take corrective action before those issues lead to downtime, lost productivity, or other costly problems.
What are the different types of preventive maintenance?
- Time-based maintenance: Time-based maintenance involves performing maintenance tasks at set intervals, such as daily, weekly, monthly, or annually. These intervals are based on manufacturer recommendations, industry best practices, or regulatory requirements.
- Usage-based maintenance: Usage-based maintenance involves performing maintenance tasks based on the amount of usage the equipment has experienced, such as the number of hours of operation, cycles, or production runs. This type of maintenance is often used for equipment that experiences heavy usage or operates continuously.
- Predictive maintenance: Predictive maintenance uses data and analytics to predict when maintenance should be performed based on the condition of the equipment. This involves monitoring equipment performance using sensors and other tools to identify patterns and potential issues before they become critical.
The type of preventive maintenance used will depend on a given business’s specific needs and circumstances. Some companies may use a combination of different kinds of preventive maintenance to achieve the best possible results.
What are the benefits of preventive maintenance?
There are several benefits of preventive maintenance, including:
- Reduced downtime: Preventive maintenance programs help to reduce equipment downtime by preventing unexpected failures and minimizing the need for reactive maintenance.
- Extended equipment lifespan: By providing the necessary maintenance, equipment will last longer, run more efficiently, and perform better.
- Improved safety: Properly maintained equipment is safer to operate, which can help reduce workplace accidents and improve overall workplace safety.
- Cost savings: By detecting and repairing issues early, maintenance costs can be kept to a minimum, saving companies time and money in the long run.
- Improved efficiency: Proper maintenance of equipment can result in better performance and reduced energy consumption, which can save money and reduce environmental impact.
- Compliance: Preventive maintenance ensures equipment complies with regulations, standards, and specifications.
Automate your preventive maintenance with SAP PM
Performing effective preventive maintenance usually involves using a Facility Management Software (FMS). A cutting-edge FMS can automate preventive maintenance tasks for you and replace bulky stacks of paper and cluttered spreadsheets. Fortunately, customers who run SAP can leverage SAP PM (Plant Maintenance) to do this heavy lifting.
SAP Plant Maintenance (PM) is an SAP Enterprise Asset Management (EAM) component that helps businesses support and maintains equipment and systems. SAP PM integrates with other EAM components like Materials Management (MM), Quality Management (QM), Production Planning (PP), Sales and Distribution (SD), Finance (FI), Controlling (CO), and Human Resources (HR).
SAP PM comprises components for the three main activities that help companies maintain systems or equipment:
- Inspection - establishes the actual condition of the systems or equipment
- Preventive maintenance - helps maintain ideal conditions for the system or equipment
- Repair - restores the systems or equipment.
Unlock the true value of your SAP EAM
Using multiple modules of SAP, such as plant maintenance and material management, during the execution of preventive maintenance can be challenging, especially for users unfamiliar with the system. According to a recent study conducted by a global IT consulting company, the integration of multiple modules in SAP can be complex, and it requires a deep understanding of the system's architecture and configuration.
The study suggests that one of the significant challenges when using multiple SAP modules for preventive maintenance is the need for data integration. For example, material management data must be linked with maintenance activities to ensure the availability of necessary spare parts during maintenance. Moreover, notifications or work orders must be generated based on the maintenance schedule or equipment condition, which can be complicated.
The study also suggests proper documentation and tracking of maintenance activities can be a significant challenge. It requires linking maintenance orders to equipment records, tracking work orders to ensure completion, and updating inventory records when spare parts are used.
Navigating these SAP modules to execute a preventive maintenance project can be challenging. Fortunately, add-on solutions, like Massetic SEAM4 and its accompanying mobile add-on solution, MOAST4, consolidate all the information from these modules into one dashboard. Such solutions can provide end-users with a more comfortable interface that enables them to:
- Consolidate information related to prerequisites needed before undertaking a maintenance project, priorities, and the availability of material and resources.
- Ensure a uniform governance mechanism where multiple teams involved in a maintenance project are always kept updated and briefed on the next steps.
- View all the necessary information related to technicians’ skill levels, availability, current load level, etc.
Therefore, the above functionalities can be used to:
- Streamline how work orders are planned
- Schedule maintenance projects with higher accuracy
- Improve technicians’ productivity
- Increase equipment uptime
In conclusion, preventive maintenance is a proactive approach to equipment maintenance, and automating these activities can help businesses maximize uptime, reduce costs, and improve productivity. By regularly inspecting and maintaining equipment, companies can prevent failures, extend equipment lifespan, improve efficiency, increase safety, and enhance regulatory compliance. Implementing a robust preventive maintenance software system is essential for any business looking to boost equipment uptime and gain a competitive edge in today's marketplace.
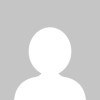